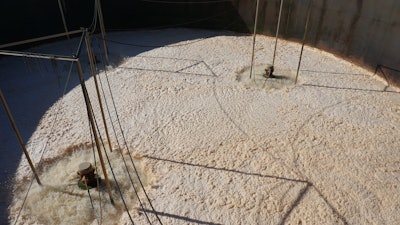
Tyson Foods Inc.’ pre-treatment operation in Berryville, Arkansas, handles high-strength wastewater from marinated and further cooked products exceptionally well.
For its performance, Tyson Foods Inc.’s operation in Berryville, Arkansas, was selected as the winner of the 2021 U.S. Poultry & Egg Association’s Clean Water Award in the pre-treatment category.
The pretreatment category covers facilities that discharge pretreated effluent to a publicly owned, full treatment facility for further treatment. To be eligible, a facility must have at least two years in which no significant non-compliances or notices of violations have occurred. Judging is based upon training, unique processes utilized for treatment, community outreach, wildlife management, water conservation and general environmental stewardship.
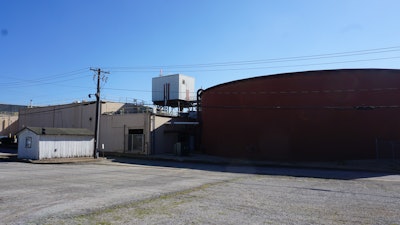
Wastewater pre-treatment
Tyson’s Berryville plant cooks 716,000 pounds of poultry products daily. Its pre-treatment operation handles about 750,000 gallons of wastewater daily. This wastewater includes food ingredients, cooking oil, animal fat, marinades and cleaning chemicals from daily sanitation. Despite this, the pre-treatment facility discharges water well below the permit limits established by its public wastewater treatment facility.
According to Tyson's application for the award, the pre-treatment facility must handle both soluble and insoluble contaminants. This means the facility must rely heavily on the biological removal of soluble contaminants to meet its permit requirements.
Insoluble contaminants are removed prior to the biological treatment process with a dissolved air floatation (DAF) process along with polymers. Soluble contaminants are removed in the 1.3 million gallon aeration basin. Solids generated from this process are removed in a second DAF and polymer treatment.
The plant is also working on upgrades that would enhance its performance including a new aeration basin and larger equalization tanks. These improvements are planned Tyson’s fiscal 2022. It may also add a screw press to reduce the amount of land applied sludge coming from the plant.
Handling oil and marinade
Berryville takes extra steps to capture harder-to-treat substances like marinades and oil.
The cooking process uses marinades, glazes, breading and batter. The facility trains workers to minimize the amount of these ingredients finding their way into wastewater collection. Because of this, about 100,000 to 150,000 pounds of these products are diverted from the wastewater stream weekly.
Cooking oil is inherently tough to filter in a fast-paced production environment. Ineffective filtration results in oil prone to scorching – because some degree of solids remain in the oil – and filtered solids which contain too much oil to be disposed of in a landfill.
In 2020, it began using a Micron-Pro Filtration Automation Inc. oil filter to replace older, inefficient filters. These units further decreased scorching issues, allowing the facility to reuse oil and reduce new oil purchases. Filter cake produced by this new process is used as an animal feed ingredient.
Tyson’s Robards facility cleans more water using less www.WATTAgNet.com/articles/41498